Vulkanisering står som en hörnstensprocess i gummitillverkning, avgörande för att omvandla rågummi till hållbara, användbara produkter. Bland de olika teknikerna som används framträder vakuumvulkanisering som en specialiserad metod med distinkta fördelar och egenskaper, som skiljer den från konventionella vulkaniseringsmetoder. Förstå de viktigaste skillnaderna mellan Vakuumgummivulkaniseringsmaskin och andra metoder är avgörande för tillverkare som vill optimera sina produktionsprocesser och uppnå gummivaror av överlägsen kvalitet.
Tryckmiljö:
Vakuumvulkanisering: Denna metod fungerar i en kontrollerad vakuummiljö, där lufttrycket sänks under atmosfäriska nivåer. Genom att avlägsna luft och instängda gaser från gummimaterialet och formhåligheten, minimerar vakuumvulkning bildandet av hålrum och luftbubblor, vilket leder till tätare och mer enhetliga produkter.
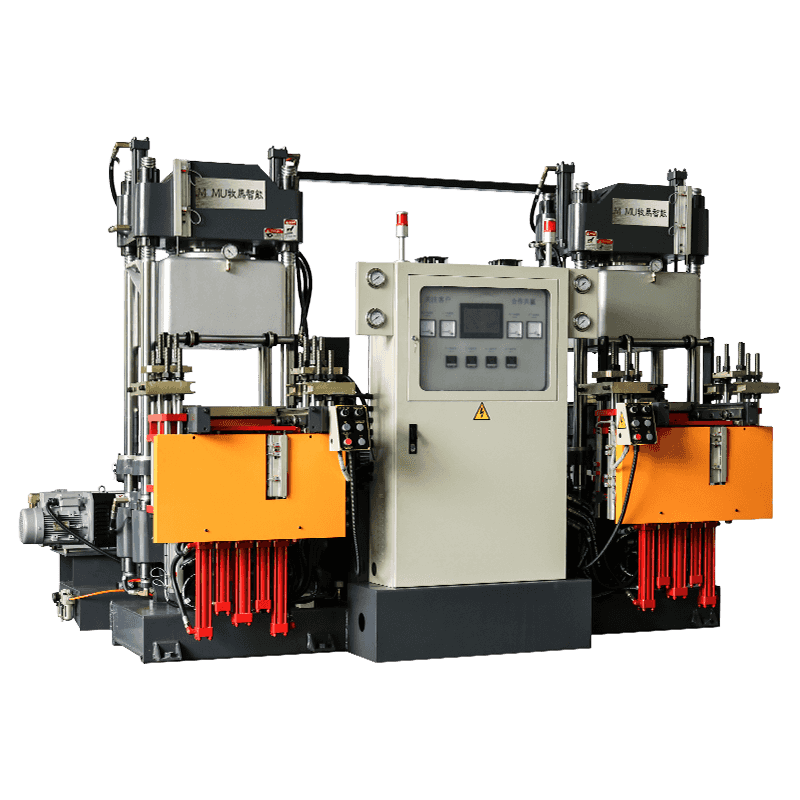
Andra vulkaniseringsmetoder: Konventionella vulkaniseringstekniker, såsom formpressning eller formsprutning, sker vanligtvis antingen vid atmosfärstryck eller under högt tryck. Även om de är effektiva, erbjuder dessa metoder kanske inte samma nivå av luftavlägsnande och kontroll som vakuumvulkanisering, vilket kan leda till inkonsekvenser i slutprodukten.
Luftborttagning:
Vakuumvulkanisering: En integrerad del av processen är den grundliga evakueringen av luft från både gummimaterialet och formhåligheten. Detta steg säkerställer att gummit är fritt från instängda luftfickor, vilket kan äventyra den strukturella integriteten och ytfinishen hos den färdiga produkten.
Andra vulkaniseringsmetoder: Även om luftavlägsnande också är väsentligt i andra vulkaniseringsmetoder, är det kanske inte så noggrant kontrollerat som vid vakuumvulkning. Följaktligen kan dessa metoder vara mer mottagliga för bildandet av lufthåligheter i gummit, vilket påverkar dess kvalitet och prestanda.
Förbättrade materialegenskaper:
Vakuumvulkanisering: Genom att eliminera luftfickor och säkerställa enhetlig materialdensitet, ger vakuumvulkning gummiprodukter med förbättrade materialegenskaper. Dessa kan innefatta förbättrad draghållfasthet, rivhållfasthet och ytfinish, vilket gör dem idealiska för applikationer som kräver högpresterande gummikomponenter.
Andra vulkaniseringsmetoder: Även om de kan producera kvalitetsgummiprodukter, kanske konventionella metoder inte uppnår samma nivå av materialkonsistens och integritet som vakuumvulkanisering. Detta kan påverka slutprodukternas hållbarhet och tillförlitlighet, särskilt i krävande eller kritiska tillämpningar.
Formdesign och komplexitet:
Vakuumvulkanisering: Vakuumvulkaniseringens specialiserade karaktär kräver ofta användningen av skräddarsydda formar utformade för att motstå vakuumtryck och underlätta effektiv luftevakuering. Dessa formar kan uppvisa större komplexitet jämfört med de som används i andra vulkaniseringsmetoder.
Andra vulkaniseringsmetoder: Beroende på de specifika process- och produktkraven, kan konventionella vulkaniseringsmetoder använda enklare formar eller verktygsdesigner. Även om de är mindre komplicerade, förblir dessa formar effektiva för sina avsedda syften men kan sakna den sofistikering som krävs för vakuumvulkanisering.
Produktionshastighet och effektivitet:
Vakuumvulkanisering: På grund av den noggranna luftborttagningsprocessen och kontrollerade härdningsförhållanden kan vakuumvulkning medföra längre härdningstider jämfört med andra vulkaniseringsmetoder. Emellertid uppvisar de resulterande gummiprodukterna ofta överlägsen materialkvalitet och konsistens.
Andra vulkaniseringsmetoder: Konventionella metoder, såsom formsprutning, kan erbjuda snabbare produktionscykler men kan offra en viss grad av materialkvalitet och enhetlighet. Valet mellan hastighet och kvalitet beror på de specifika tillverkningskraven och önskade slutproduktegenskaper.